Digitalizzare i processi produttivi non significa solo trasformare i processi aziendali tradizionali introducendo tecnologie digitali, come software, sistemi informatici e automazione. Un percorso di digitalizzazione efficace prevede di efficientare il lavoro lungo tutto il percorso dello sviluppo di un prodotto mediante l’uso di tecnologie interconnesse tra loro.
Dalla teoria alla pratica: i passi da compiere
Convertire i dati, documenti e attività in formati digitali prevede un percorso che implica diverse scelte. Vediamo i passi necessari.
- Automatizzare le attività manuali e ripetitive per ridurre gli errori umani e aumentare l’efficienza. Il tempo liberato potrà essere dedicato a compiti più creativi e ad alto valore aggiunto.
- Consentire l’accesso da remoto dei dati. La possibilità di accedere da parte di tutte le figure professionali interne all’azienda ai progetti, ai dati e ai documenti da qualsiasi luogo e in qualsiasi momento consente una maggiore flessibilità e facilita la collaborazione tra team distribuiti geograficamente.
- Contenere l’uso della carta: oltre a ridurre l’impatto ambientale, evita onerosi costi di gestione dell’archiviazione.
- Snellire il monitoraggio e l’analisi dei dati per identificare tendenze, inefficienze e opportunità di miglioramento dei processi.
Ecosistemi eterogenei frenano il cambiamento
Questo cambio di paradigma nei processi produttivi spesso si scontra con una cultura imprenditoriale conservativa e con i falsi miti che si alimentano vicendevolmente all’interno di tutti gli ecosistemi aziendali, di grandi e piccole dimensioni.
Tra i problemi reali troviamo lo scarso grado di apertura al cambiamento e all’innovazione, in particolare delle figure apicali, ma anche la mancanza di competenze digitali. La carenza di personale specializzato è, infatti, un problema nazionale. Lo conferma un’indagine di Unioncamere effettuata a gennaio su un campione di 121.000 imprese appartenenti a tutti i settori industriali e dei servizi. L’area tecnica e della progettazione rappresenta il 67,9% della ricerca di personale da parte delle industrie che vede per il 47,7% figure di progettazione e ricerca e sviluppo, l’80,3% lavoratori specializzati nell’installazione e manutenzione, il 45,4% di professionisti addetti alla certificazione e controllo qualità, sicurezza ambientale.
Tra i falsi miti troviamo invece l’illusione che acquistare un software garantisca la digitalizzazione. Il mercato offre infinite possibilità: tante sono le esigenze e ogni criticità o obiettivo da raggiungere fa storia a sé. La consulenza di esperti in grado di valutare i pro e i contro di una tecnologia può fare la differenza sulla riuscita dell’intero progetto di transizione digitale. L’adozione, ad esempio, di diversi software performanti ma scollegati tra loro potrebbe rivelarsi un investimento costoso e inefficace che va a creare ulteriore complessità.
Digitalizzare i processi produttivi: le esperienze di Arena, F.lli Rossetto ed e-Novia
Come esempi di approccio corretto alla trasformazione digitale dei processi, citiamo tre casi di successo che arrivano da realtà molto diverse tra loro: Arena il noto brand per lo swinwear, F.lli Rossetto azienda veneta artigianale impegnata nel settore arredamento e una giovane start up, e-Novia, che opera nella robotica veicolare e collaborativa; rappresentano l’approccio corretto alla trasformazione digitale dei processi.
Per tutte le imprese, le fasi di scounting dei software e la selezione del system integrator più affidabile sono state cruciali. La scelta di TS Nuovamacut, gruppo TeamSystem, e della tecnologia 3DExperience Platform di Dassault Systèmes si sono rivelate vincenti, come confermano i risultati raggiunti e delle testimonianze raccolte.
Tra gli obiettivi di Arena c’era la riduzione del proprio impatto ambientale e rendere più snello e veloce il processo che va dall’ideazione alla produzione dei propri capi e accessori. Con l’adozione della 3DExperience Platform, che offre funzionalità collaborative e di simulazione, è stato possibile effettuare test real time delle performance di ciascun prodotto già in fase di progettazione.
La condivisione dei dati e delle informazioni tra i vari reparti ha migliorato la qualità del prodotto senza contare il risultato eccellente che riguarda l’abbattimento del 70% della produzione di prototipi fisici. Come afferma Loris Vallesi, Head of IT & Business Solutions di Arena, «simulando tutto nel nostro ufficio di progettazione, non dobbiamo creare più campioni di prodotto o utilizzare campioni di prodotti di terzi, riducendo così le nostre emissioni di CO2. I flussi di lavoro migliorati ci aiutano a fornire prestazioni, stile, comfort e vestibilità ai clienti, integrando la sostenibilità nel processo».
Who's Who
Loris Vallesi
Head of IT & Business Solutions di Arena
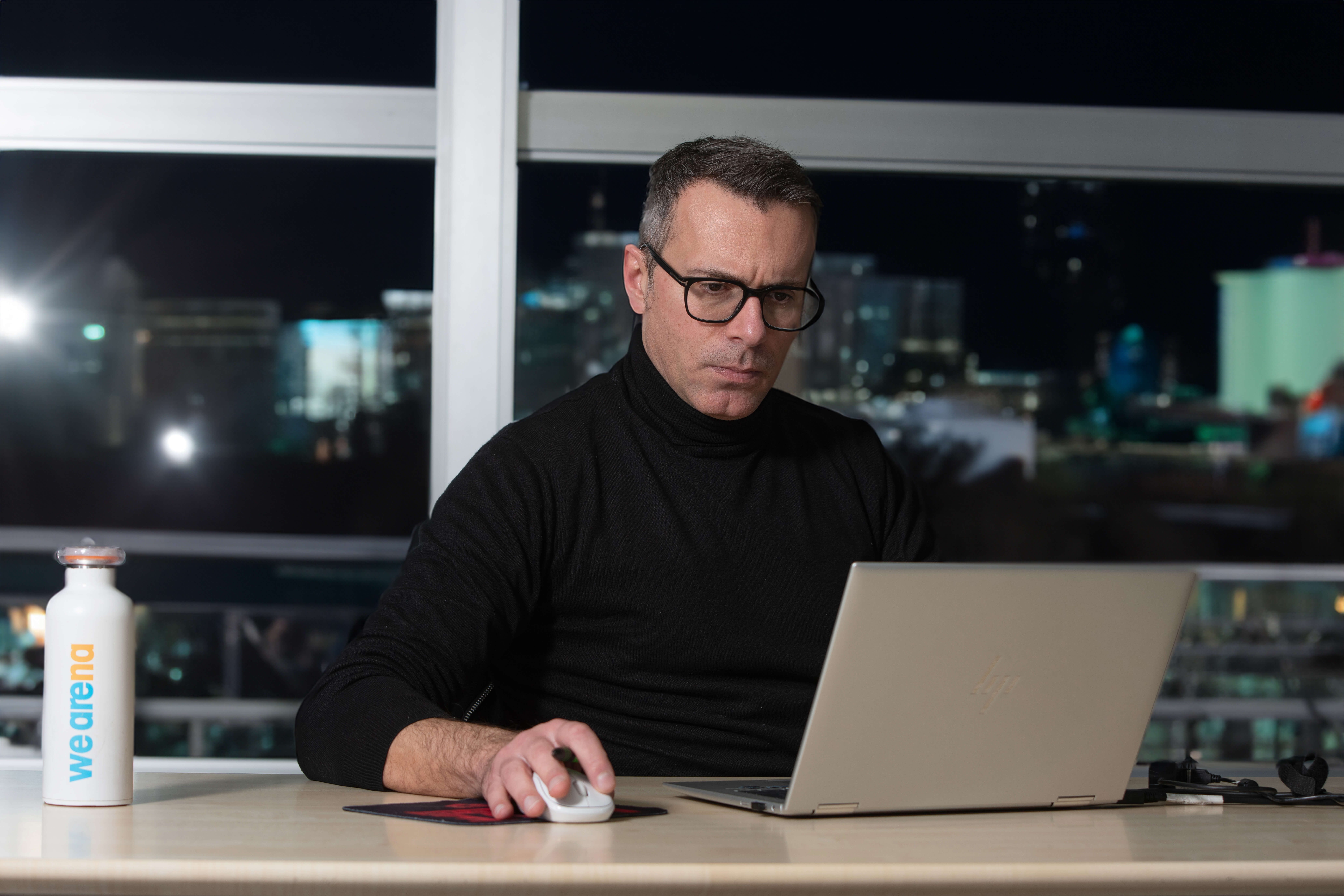
La riduzione dei costi e tempi di progettazione è infatti tra i desiderata di tutte le aziende. Per F.lli Rossetto, ad esempio, la gestione di oltre 500 mila modelli di sedute, esportate in 60 paesi di tutto il mondo, stava diventando onerosa: servono server sempre più potenti, mentre i dati a volte non aggiornati, sparsi in tante cartelle non condivise, e workflow aziendali poco chiari rappresentavano un rischio di errore davvero alto. Con l’uso della 3DExperience Platform è stato possibile tracciare l’80% del processo produttivo, grazie alla definizione di un workflow strutturato in task, la centralizzazione delle informazioni e l’eliminazione dello scambio di mail o file.
Tutto il know how aziendale è stato concentrato in un unico ambiente di lavoro in cloud. Un risultato soddisfacente, come afferma Marco Rossetto, Responsabile R&D: «la condivisione del dato è una leva importante: l’allineamento dei nostri manager, grazie a strumenti come la 3DExperience, ci consente di raggiungere gli obiettivi aziendali».
Who's Who
Marco Rossetto
Responsabile R&D F.lli Rossetto
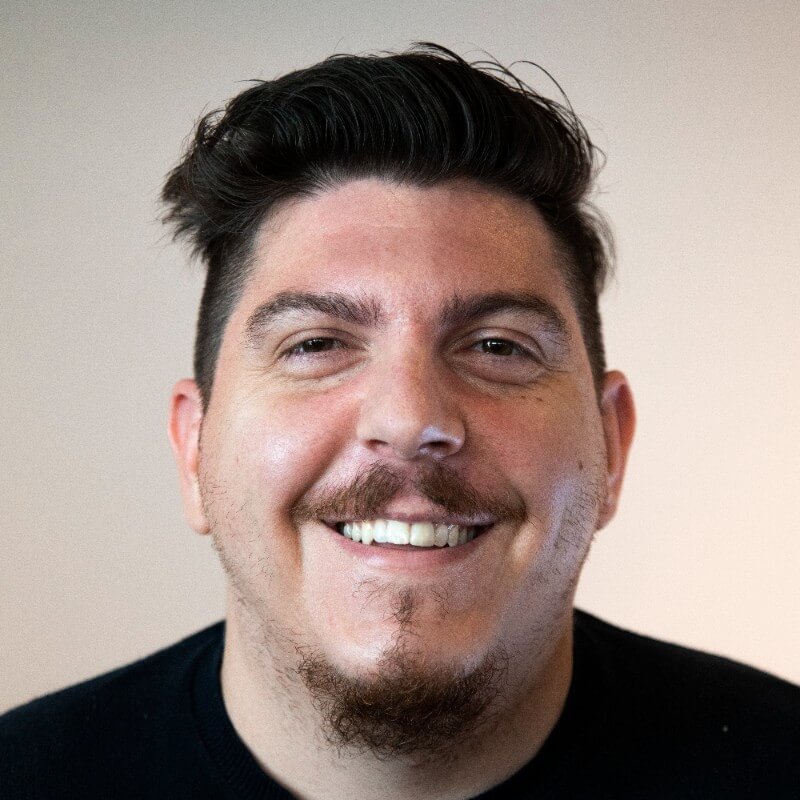
Per la start up e-Novia, invece, è stata l’esigenza di accelerare il proprio time to market l’opportunità per esplorare le funzionalità della 3DExperience. In questo caso specifico è stata utilizzata per la realizzazione di una scarpa che restituisce un’analisi biomeccanica del piede, grazie a un sistema elettronico integrato nella suola. La realizzazione di un prodotto così innovativo ha richiesto un approccio multidisciplinare; da subito si è presentato il problema di gestire lo scambio di idee e competenze, oltre che un aggiornamento costante sullo stato di avanzamento della progettazione, simulazione e modellazione. L’introduzione della piattaforma collaborativa di Dassault Systèmes ha abbattuto i tempi di realizzazione da 14 mesi a 8 mesi, collegando l’intera rete di stakeholders che poteva accedere ai dati necessari in ogni momento da qualsiasi luogo.
Da questi esempi si conferma che le tecnologie abilitanti rappresentano un buon investimento solo se migliorano l’efficienza strategica e l’operatività. La scelta di software performanti non basta.
L’esperienza di queste aziende è la testimonianza concreta che avere un unico ambiente di lavoro collaborativo e integrato lungo l’intero processo di sviluppo prodotto è il requisito indispensabile per prendere decisioni intelligenti in tempi brevi ed essere davvero competitivi.