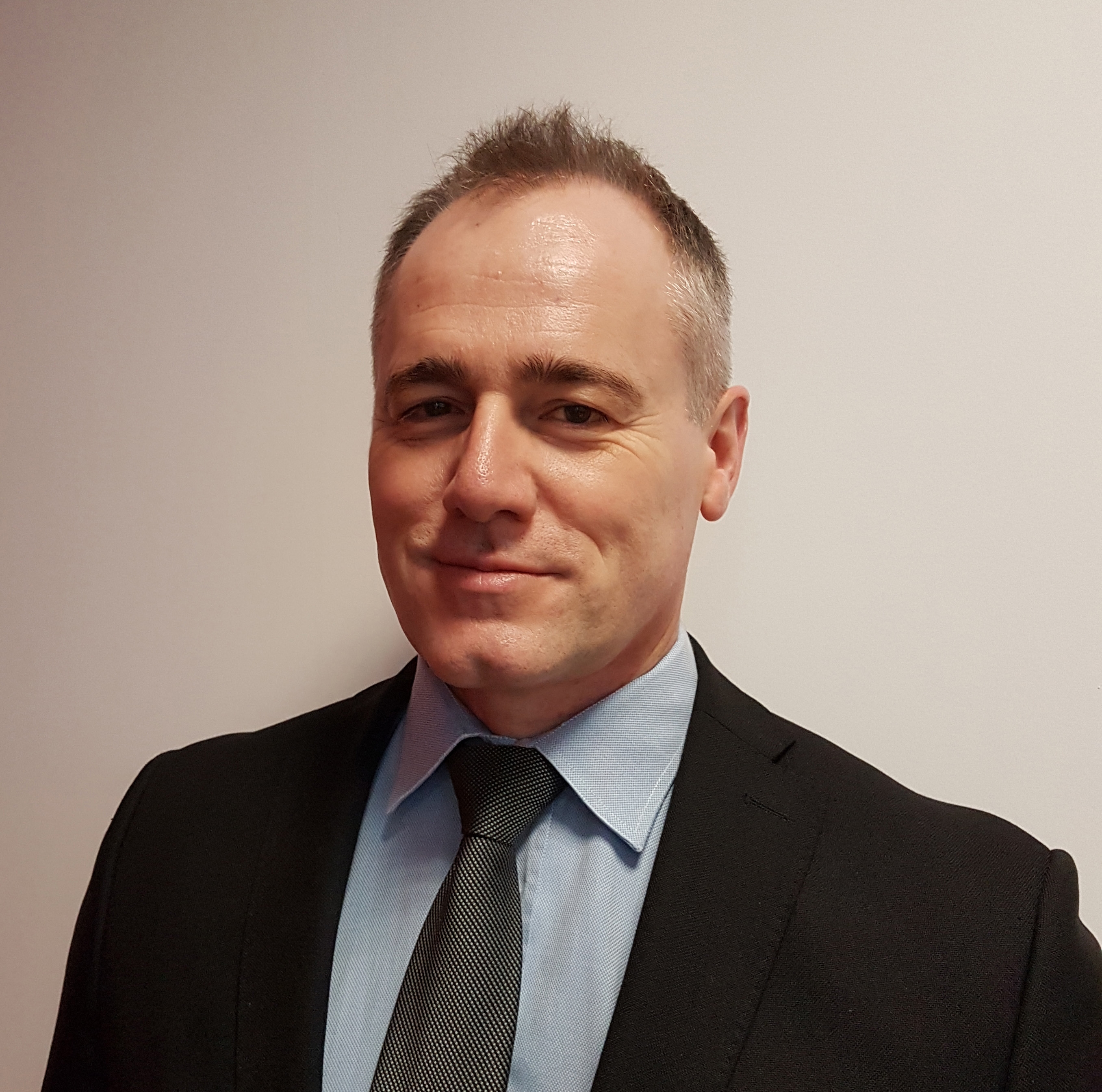
Uno strumento per “chiudere il cerchio” nella gestione di produzione e supply chain, e completare il sistema ERP/PLM in tutto il mondo. Questo in poche parole è il progetto in corso in Comau, società del gruppo Fiat Chrysler tra i leader mondiali dell’automazione industriale, per implementare un sistema SRM (Supplier Relationship Management).
«L’obiettivo – ci spiega il CIO Flavio Bernocchi – è migliorare collaborazione e condivisione di informazioni con i fornitori, pianificazione degli acquisti di materiali e prodotti, e gestione del conto lavoro. E di conseguenza sia i tempi di consegna che la qualità dei prodotti. È una tappa importante nel percorso che Comau sta facendo verso Industria 4.0, la Smart Factory, e la distribuzione digitale della conoscenza nella supply chain integrata».
Comau nasce nel 1973 come Consorzio Macchine Utensili, ha sede a Grugliasco (Torino) ed è presente in 17 paesi in tutto il mondo, con 33 location – di cui 5 centri di innovazione e 15 stabilimenti – e 12.600 persone. Il fatturato ha sfiorato nel 2015 i 2 miliardi di euro: sempre in crescita negli ultimi anni, proviene da tutte le 4 regioni mondiali (dal 38% in EMEA al 13% in Asia-Pacifico), ed è “captive” per circa il 25-30%: «Per il resto lavoriamo con tutti i principali costruttori auto, da Tesla, a Ford a General Motors a Mercedes, e con diversi altri settori manifatturieri».
«Un discorso di time-to-market, ma anche di qualità»
Il gruppo fa prodotti (come i robot industriali) e sistemi di automazione industriale, progettando e realizzando linee di produzione e montaggio da installare negli stabilimenti dei suoi clienti, con frequenti modifiche di specifiche e disegni. Essere sempre allineati con i fornitori sull’ultima versione di un disegno, sottolinea Bernocchi, con un workflow che assicura risposte immediate, è fondamentale per la pianificazione, soprattutto nelle grandi commesse.
«In un sistema ben ingegnerizzato basta che un solo fornitore ritardi, e anche il componente più piccolo diventa critico: ci serviva un sistema SRM per portare online tutti i fornitori». È un discorso di time-to-market, ma anche di controllo della qualità. «Quasi sempre prima di portare la linea al cliente la testiamo in casa, perché occorre essere sicuri che tutto funzioni già prima. Raramente ormai i clienti partono da zero, con uno stabilimento vuoto. In una fabbrica automotive quando si dismette un modello, si smonta la relativa linea e si monta quella del nuovo modello: i tempi a disposizione sono brevi».
Il progetto tocca molti paesi in cui è presente Comau (USA, Messico, Italia, Romania, Brasile, Argentina, UK, Germania, Francia, Cina, India e Polonia), e prevede due fasi. La prima, che si concentra sulle funzioni base del sistema, si concluderà per la regione EMEA ad aprile 2017, e per tutto il mondo a metà 2018. «Per ora sono coinvolti 200 fornitori per ogni region, circa un terzo del parco fornitori Comau. Poi estenderemo anche ai più piccoli. Sono esclusi i fornitori grandi, che integreremo direttamente con un portale, più avanti».
Uno “scoring” dei fornitori sempre più preciso
Il sistema, precisa Bernocchi, è pensato per essere “pervasivo”: «L’approccio è di supply chain management esteso, dato che arriviamo anche al warehouse management e al manufacturing». Già dalla fase 1 quindi sono coinvolti tutti i processi operativi: dall’order management, con RFQ verso i fornitori e tutto ciò che è correlato («per esempio l’emissione dell’ordine integrato con SAP»), alla gestione del follow-up, cioè dei workflow di riprogrammazione necessari in caso di modifiche («spesso i fornitori sono in conto lavoro, quindi è complicato chiudere il giro»). Poi ci sono funzioni di document exchange («soprattutto disegni dal PLM»), e di “delivery enhancement”, come l’advanced shipping, che quando arriva un componente ne accelera l’inserimento nei sistemi informativi aziendali.
Nei piani di Comau il SRM, basato su tecnologie dell’italiana Tesisquare, completa insomma una piattaforma con altri due capisaldi: l’ERP (SAP) e il PLM (Enovia di Dassault Systemes). «Il SRM dev’essere strettamente integrato con il PLM per la gestione di disegni e distinte, e con l’ERP per la pianificazione dei materiali, l’entrata merci, la logistica e il manufacturing».
La fase 2 del progetto, poi, introdurrà funzionalità di analisi (Supplier Scorecard, Ranking, Payment & Contract, Qualification Process).«Abbiamo già possibilità di analisi a livello strategico nei sistemi di business intelligence, ma avevamo bisogno anche di un livello operativo quotidiano. Questo costituisce la seconda fase perché preferiamo prima acquisire familiarità con il sistema e usare i suoi standard, invece di impostare tutto solo in base alla teoria».
L’obiettivo qui sarà definire in dettaglio la “qualità” del fornitore in senso lato. «Avremo molti indicatori su tempi, costi e altre variabili, da integrare con i dati ERP sulla qualità dei componenti, e con valutazioni qualitative del follow-up, per avere uno scoring dei fornitori sempre più preciso, e in futuro automatizzare azioni come per esempio il “blocco” di un fornitore che scende sotto certi valori di soglia, ovviamente con tutte le attenzioni del caso».
Quanto alla scelta della tecnologia, «soprattutto per le commesse, la gestione solo su ERP e PLM non bastava. Così abbiamo cercato una soluzione che offrisse soprattutto funzionalità di supply chain management sulle commesse rispondenti ai nostri requisiti, più che referenze internazionali: nella gara ha prevalso Tesisquare».
Nella software selection sono state valutate anche soluzioni “pure cloud”, «ma la condivisione di file molto pesanti come i disegni 3D può diventare complicata se i server sono lontani, per esempio in California. I tempi di latenza sarebbero troppo lunghi: tendendo verso la Digital Factory, queste informazioni saranno sempre più pesanti, presto stamperemo anche in 3D, per cui questo è un elemento critico».
I fronti d’investimento Industria 4.0: IoT, Big Data, wearable e Cloud
Comau sta gestendo il progetto direttamente, insieme a Tesisquare. Lo staff IT nella multinazionale torinese è formato da circa 100 persone sparse in tutto il mondo: «In questo momento, a parte il SRM, stiamo lavorando per completare i roll-out del consolidamento di quello che chiamiamo GPS, Global Process System, che integra ERP e PLM, e poi stiamo portando avanti alcuni componenti di Digital Factory, tipicamente di IoT (Internet of Things) per le linee di produzione e per prodotti come gli AGV wireless, carrelli robotizzati totalmente controllabili da remoto che “capiscono” l’ambiente circostante».
Comau, conclude Bernocchi, sta investendo in modo rilevante sull’IoT, soprattutto sulla sensoristica per i robot, e su analytics e Big Data per elaborare questi dati. L’obiettivo è definire un modello di manutenzione predittiva. «Quanto al Cloud, stiamo cercando di capire, man mano che le varie soluzioni maturano, cosa possiamo portare fuori dai nostri data center – dati e applicazioni – compatibilmente con le esigenze di latenza zero e la sensibilità di alcuni tipi di dati dei clienti».
Anche i wearable sono un fronte attivo di investimenti: «Per gli addetti di stabilimento, dopo un primo test negativo sugli occhiali – per ora percepiti come troppo invasivi – stiamo sperimentando “orologi” con input basici per il controllo qualità sulle linee, e “guanti” che informano sulle operazioni da fare. Ma siamo solo all’inizio».