Anche l’area produzione e logistica delle aziende, le cosiddette Operations, sta vivendo la trasformazione digitale, e questa tendenza in Italia è più che mai attuale, grazie al Piano Nazionale Industria 4.0 varato nel settembre 2016.
Il recente Workshop organizzato dalla Digital Transformation Academy della School of Management del Politecnico di Milano presso la sede centrale di Bayer Italia, a Milano, è stato l’occasione per farsi un’idea precisa di come una delle multinazionali più radicate in Italia in termini di Operations locali stia affrontando questa fase cruciale.
«Bayer ha oltre 150 anni, è cambiata molto nel tempo e oggi si occupa di Life Sciences nel senso più ampio: scienza della vita per uomini, animali e piante», ha detto Paolo Zanzi, Head of Quality Organization and Innovation di Bayer, introducendo l’evento. «Ha circa 100mila dipendenti, quasi 35 miliardi di euro di fatturato e 4,4 miliardi di investimenti in Ricerca e Sviluppo. In Italia abbiamo oltre 2mila persone, oltre un miliardo di fatturato, tre siti produttivi e anche Centri di ricerca. L’innovazione è la nostra “core competence”, che, oltre agli investimenti economici, affrontiamo con un approccio al cambiamento basato su 4 pilastri: sperimentazione, customer focus, trust, collaborazione».
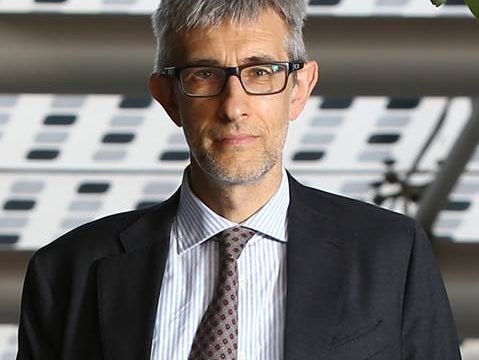
Dei progetti di gestione dei trasporti e delle consegne raccontati al workshop da Michele Palumbo, Head of Supply Chain Management, abbiamo parlato in un articolo a parte qualche giorno fa. Oggi invece approfondiamo l’impegno di Bayer Italia in campo Smart Manufacturing / Industria 4.0 emerso dalla testimonianza di Daniela Galli, Responsabile di Produzione dello Stabilimento Bayer di Garbagnate (Milano). Lo stabilimento ha circa 280 dipendenti ed è specializzato nella produzione e confezionamento di farmaci in forma solida orale (compresse e microcapsule) distribuite in Italia e all’estero.
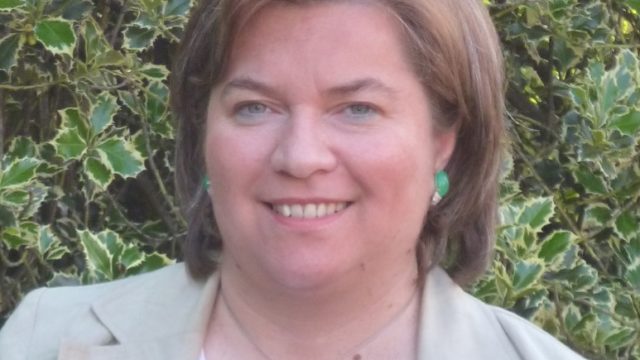
«Per dare un’idea del significato di Industria 4.0 per uno stabilimento produttivo partiamo da due esempi pratici. Il primo è una linea di confezionamento dotata di un gran numero di sensori tramite cui comunica con il sistema di pianificazione della produzione, inviando segnali sullo stato di funzionamento o di fermo per guasto o manutenzione». In caso di fermo – continua Galli -, il sistema rischedula il prossimo ordine di produzione su altre linee, con ottimizzazione automatica di macchine e persone. «Un altro esempio riguarda la supply chain, l’integrazione tra i sistemi informativi del produttore di farmaci e quelli del fornitore del materiale di confezionamento: se quest’ultimo ha visibilità sul piano di produzione del primo, farà arrivare i componenti nel momento giusto, con riduzione delle scorte e minor capitale circolante».
Altre applicazioni Industria 4.0 che Bayer sta studiando riguardano le macchine: la manutenzione predittiva e l’assistenza da remoto. Nel primo caso si parla di monitoraggio del comportamento di un impianto attraverso sensori, con l’idea di intervenire non secondo uno scadenziario predefinito, indipendentemente dallo stato di usura di un componente, ma quando specifiche variabili superano definite soglie di rischio. «Per esempio, se sì è accertata una correlazione tra la presenza di parti metalliche nell’olio di lubrificazione e probabilità di guasto di un motore, si può fare in modo che al raggiungimento di un valore soglia stabilito si generi una richiesta automatica di intervento di manutenzione», prosegue Galli.
Assistenza da remoto, enormi i potenziali benefici
Quanto all’assistenza da remoto, «a Garbagnate è un tema di vivo interesse: certo, la connessione con l’esterno pone sfide di cybersecurity, però i vantaggi in termini di abbattimento dei tempi di intervento sono enormi: il produttore di una nostra macchina, connesso in remoto, in caso di problemi può fare una diagnosi, e a volte anche risolverli senza dover mandare tecnici. Ricordo qualche anno fa un fermo di 5 giorni di una stazione di pesatura per un problema software: se il produttore fosse stato connesso da remoto avremmo risolto in 3-4 ore», sottolinea la manager.
Dall’intervento di Galli emerge come Bayer stia lavorando – con stati d’avanzamento diversi – su tutte le tecnologie Industria 4.0. Nell’area Advanced HMI (Human Machine Interface), per esempio, presto a Garbagnate saranno implementati degli “smart glasses”, occhiali a realtà aumentata che proiettano direttamente sul pezzo meccanico le operazioni da eseguire, con riduzione dei tempi di intervento e delle possibilità di errore.
Altri fronti sono l’Additive Manufacturing, cioè la Stampa 3D in ambito produttivo («è già realtà in alcuni stabilimenti Bayer, per produrre prototipi o componenti») e i pallet/carrier intelligenti: contenitori abilitati da RFID, che scambiano, con i sistemi MES, ERP e di Inventory Management, informazioni in tempo reale sul proprio peso (e quindi percentuale di riempimento) e localizzazione. «È un passo avanti rispetto alla situazione attuale perché al raggiungimento di una soglia di carico i segnali fanno scattare nel sistema gestionale il riordino del materiale; altro vantaggio è l’allineamento in tempo reale tra giacenza fisica e contabile», commenta Daniela Galli.
Con McKinsey un progetto Big Data sulla fabbrica del futuro
Infine l’area Big Data e Advanced Analytics: «A Garbagnate stiamo portando avanti con McKinsey un progetto pilota di fabbrica del futuro per l’intera Bayer, un’iniziativa entusiasmante che ci rende orgogliosi», spiega Galli. L’obiettivo è cercare correlazioni tra dati provenienti dai sistemi più diversi: ERP, MES, LIMS (analisi chimica e microbiologica dei prodotti), software degli impianti produttivi (linee di confezionamento, granulatori, comprimitrici, bassine…), software di analisi delle deviazioni di produzione, software di raccolta dati di produttività e analisi dei fermi, software di gestione della formazione degli addetti etc… allo scopo di migliorare, in ultima istanza, la produttività dello stabilimento.
«I benefici attesi dall’Advanced Analytics sono ampi: prima di tutto potremo avere in tempi molto più rapidi il risultato di analisi di problemi e situazioni riscontrate, indicazioni su come migliorare la produttività, quando eseguire la manutenzione, quali materiali di quali fornitori preferire, o anche come indirizzare la formazione del personale».I
I benefici attesi: dai KPI in tempo reale alla produzione custom con costi di massa
In generale, sottolinea Galli, da investimenti e progetti nell’ambito Industria 4.0 Bayer si aspetta molti tipi di benefici: alta flessibilità; dati di produttività ed efficienza in tempo reale; riduzione delle deviazioni di produzione; capacità di produzione customizzata, cioè di lotti piccoli in condizioni economiche di produzioni di massa; migliore pianificazione, e quindi riduzione di scorte e capitale circolante; disponibilità in tempo reale di KPI sullo stato di impianti e processi; tempi di attraversamento (cioè cicli di produzione) più veloci.
«L’anno scorso Bayer ha investito 11 milioni di euro a Garbagnate: risorse che comunque sarebbero state investite, ma il Piano Nazionale Industria 4.0 ha accelerato il processo decisionale – ha concluso Galli -. Occorreranno molti investimenti, anche sulle risorse umane, con sviluppo di competenze nuove, riconversione di quelle esistenti, flessibilità lavorativa con più focus su responsabilità e risultati, e meno su presenza fisica. Sarà necessario aumentare la sicurezza della rete informatica: dovremo individuare punti deboli, alzare i livelli di protezione, soprattutto per le informazioni sensibili, tutelare il know-how aziendale e fare formazione per creare consapevolezza negli operatori, fornendo loro best practice».