«La siderurgia non è un settore “glamour”: è considerato old economy e avverso all’innovazione. Ma le cose stanno cambiando, perché anche in un settore del genere la trasformazione digitale offre molte opportunità di forti benefici e vantaggi competitivi». Così Alberto Messaggi, CFO di Feralpi Group, introduce il piano di profonda innovazione che la multinazionale lombarda ha avviato quattro anni fa con l’implementazione di un sistema ERP, e che sta proseguendo con diversi progetti basati su tecnologie digitali.
Feralpi è nata esattamente 50 anni fa a Lonato del Garda, ed è cresciuta nel tempo, anche grazie ad acquisizioni, fino a diventare oggi un gruppo da 1,3 miliardi di euro di fatturato (64% all’estero) e 1400 dipendenti in vari paesi europei e nel Nord Africa, con 14 stabilimenti in Italia, 6 all’estero, e 6 società commerciali e di servizi in altrettanti paesi.
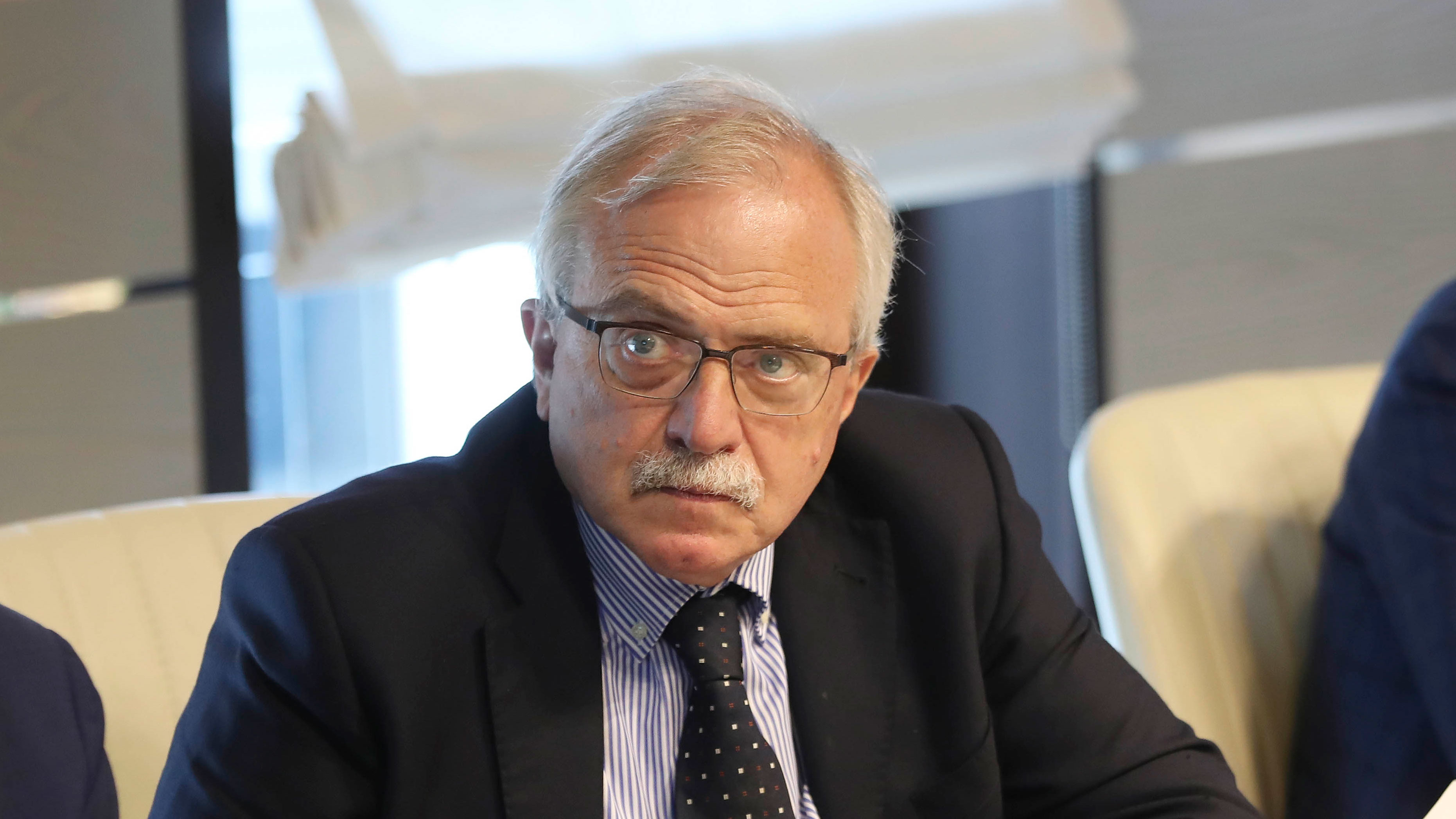
«Stiamo valutando o implementando diverse tecnologie digitali, dalla robotica alla realtà aumentata, dalla stampa 3D all’Internet of Things», precisa Messaggi, che abbiamo intervistato a margine dell’evento SAP NOW, dove era uno degli speaker della sessione plenaria. «L’idea è di fare innovazione di prodotto – per esempio recinzioni “intelligenti” con sensori che segnalano scavalcamenti – ma soprattutto innovazione di processo. La tecnologia a più alto impatto su cui stiamo lavorando è quella dei big data analytics per l’ottimizzazione dei processi, perché i nostri processi sono instabili per definizione. Dipendono da tantissime variabili e si svolgono in condizioni ambientali estreme».
Le singole fasi per l’efficienza, l’intero processo per la qualità
Se persino attaccare un’etichetta a un fascio di cavi è complicato quando il fascio è a una temperatura di 1200 gradi, continua Messaggi, nel caso del forno, che è il cuore del processo di produzione nella siderurgia, il livello di complessità diventa altissimo. «Ma oggi è possibile anche governare un ambiente del genere, per cui non ci sono formule univoche e definitive, se si possono generare grandi moli di dati di monitoraggio e si dispone di una capacità di profonda analisi».
L’obiettivo ultimo a cui punta Feralpi è riuscire a monitorare l’intera catena di produzione con una visibilità complessiva. «Il progetto più interessante che abbiamo in corso in effetti cerca di seguire tutto il processo di produzione dall’acciaieria di Calvisano attraverso diverse società del gruppo, fino al cliente. Recentemente abbiamo comprato alcune società specializzate in acciai speciali, produzione che necessita di un livello di qualità del prodotto più alto dell’acciaio tradizionale. Abbiamo quindi bisogno di tracciare la produzione e i livelli qualitativi lungo tutte le fasi del processo».
Messaggi si riferisce al progetto “Quality Integration”, un piano pluriennale “Industria 4.0” di digitalizzazione del processo produttivo per tracciare i prodotti, efficientare i processi e aumentare i livelli di qualità. Dal punto di vista tecnologico, Quality Integration si baserà a regime su un ambiente con SAP Cloud Platform (analytics), Future One Dynamic Steel (piattaforma predictive basata su tecnologie in-memory e motore di machine learning), e SAP Leonardo (IoT), a cui si connettono automazione di fabbrica, impianti, linee di lavorazione, fornitori, clienti e addetti, nonché SAP ERP come “digital core”.
«L’idea è appunto di ottimizzare singole fasi, ma anche l’intera linea. Non ha senso a questo punto ottimizzare la produzione in un sito, nell’ambito di un ciclo di supply chain che ottimizzato non è». E non è un discorso solo di costi ed efficienza, ma soprattutto di qualità del prodotto. «Per noi è fondamentale, nel caso un cliente segnali un difetto, risalire alla fase in cui è verificato e al motivo. E poi molti clienti fanno ulteriori lavorazioni, per cui hanno bisogno di dati tecnici relativi alla colata e al nostro processo di lavorazione».
Più in generale il tracciamento permette di dimostrare cosa si è fatto, quando, e come, a quali trattamenti è stato sottoposto il prodotto, al limite anche poterlo certificare, e questo può fare la differenza quando si lavora per settori ad altissime specifiche come per esempio l’automotive.
La difficoltà principale non è raccogliere i dati, è definire gli algoritmi
Per ora comunque la fase su cui il progetto è più avanzato è la colata continua: «Prima l’operatore poteva gestire 6-8 variabili: a regime arriveremo a 300, il che significa un controllo capillare. Il sistema può già apprendere e lavora per eccezioni al superamento di limiti prefissati di alcune variabili». Successivamente il team di progetto si concentrerà sulle fasi a valle. «Credo che ci vorranno un paio d’anni, non è semplice. Per esempio nel caso del forno, la difficoltà principale sono gli algoritmi: non basta mettere dei sensori, occorre capire come interpretare i dati che arrivano dai sensori, e usare l’elaborazione dell’algoritmo come input per decisioni e azioni successive».
Ma Quality Integration come accennato non è l’unico progetto digitale in corso nel gruppo. «Sempre nell’acciaieria di Calvisano ne sta partendo uno che fa un’analisi “intelligente” del rottame, che è la nostra materia prima. Concettualmente questo progetto si colloca a monte delle fasi coperte da Quality Integration, e chiude il cerchio. L’obiettivo è arrivare a un sistema che riesca a classificare il rottame in entrata per tipologia, e all’interno di questa per qualità. Ed è difficilissimo, perché lo stato e la composizione del rottame è imprevedibile con metodi tradizionali».
Altri due progetti interessanti sono in Feralpi, che è l’altra principale acciaieria del gruppo. «Uno è dedicato alla creazione di un portale per inserire gli ordini online, e ripianificare i flussi in funzione di questi ordini. Un altro su cui stiamo lavorando da tempo e siamo arrivati a un discreto livello riguarda la gestione delle manutenzioni delle macchine. Avevamo già un sistema a questo scopo, adesso ne stiamo sviluppando un altro più sofisticato che parte dalla percezione delle vibrazioni delle macchine in modo da capire quando sia necessario intervenire, con un approccio reattivo invece che di manutenzione programmata».
Infine abbiamo chiesto a Messaggi perché un Chief Financial Officer per raccontare di progetti di tecnologie digitali all’evento di un vendor tecnologico. «Ho anche altre cariche nel gruppo oltre a quella di CFO, ma non è questo il punto. Questo tema mi interessa, ho sempre seguito l’evoluzione di questo tipo di progetti, perché il processo di innovazione non può essere legato solo alla funzione produzione. Deve essere condiviso. Un manager a un certo livello deve saper capire tutte le direttrici d’azione dell’azienda, non può pensare solo alla sua area. Non è un caso che fino a qualche anno fa a questo tipo di eventi veniva il CIO, mentre oggi vengono anche responsabili di linea di business o amministratori delegati: è perché i progetti di trasformazione digitale sono diventati critici. Non hanno più soltanto impatti circoscritti o di efficienza: hanno impatti strategici».