Le imprese italiane di manufacturing hanno sempre puntato storicamente sulla progettazione e sviluppo dei prodotti per creare vantaggi competitivi, ma la globalizzazione dei mercati e i profondi impatti della crisi economica hanno reso ancora più cruciale questo aspetto per distinguere il ‘made in Italy’ nel mondo.
Con questa convinzione la School of Management del Politecnico di Milano, in collaborazione con docenti e ricercatori di altri atenei italiani (Università degli Studi di Bergamo, Brescia, Firenze, Roma ‘Tor Vergata’, Salento, Università Politecnica della Marche) ha creato l’Osservatorio GeCo (Gestione dei Processi Collaborativi di Progettazione), che proprio in questi giorni ha presentato la sua prima indagine.
Il lavoro dei ricercatori ha preso in esame 103 imprese manifatturiere italiane (44 PMI sotto i 250 addetti e 59 grandi imprese sopra tale soglia) di 20 settori industriali, tra cui Meccanica, Componentistica, Impiantistica, Elettrodomestici, Elettronica, Tlc, Chimica, Alimentare, Tessile e Moda. Oltre il 60% opera per clienti aziendali, lavorando in oltre l’80% del casi a commessa, circa il 90% opera sui mercati internazionali per una quota rilevante del fatturato, e oltre il 70% realizza prodotti e sistemi di alta complessità, con centinaia o migliaia di componenti.
Concurrent Engineering, tra il dire e il fare…
Si tratta quindi, spiegano i ricercatori, di un campione rappresentativo della realtà manifatturiera italiana, con imprese che si giocano la propria competitività su scala internazionale, spesso leader di nicchia, con un buon livello organizzativo generale. Approfondendo però la gestione dei processi di progettazione e sviluppo, emergono spesso le tipiche contraddizioni del tessuto industriale italiano.
Da una parte infatti, spiega Monica Rossi, Responsabile della Ricerca dell’Osservatorio, “il campione mostra una discreta maturità nell’esecuzione del processo di sviluppo del prodotto: l’80% monitora le prestazioni in quest’ambito, il 70% punta a un miglioramento continuo, e l’80% applica un approccio di Concurrent Engineering, parallelizzando le varie fasi del processo e promuovendo collaborazione e condivisione delle responsabilità, cosa che permette a chi progetta di avere presenti tutte le fasi del ciclo di vita del prodotto”.
Dall’altra però, l’applicazione pratica di questi principi non è molto coerente, spiega Sergio Terzi, Direttore del Comitato Operativo dell’Osservatorio. “Metà del campione punta sulla massima flessibilità del processo e l’altra metà cerca di gestirlo con estrema regolarità; nel 50% delle imprese le modifiche nel processo di sviluppo sono continue, mentre l’altra metà prevede modifiche solo nelle primissime fasi; e infine nel 60% dei casi è ben chiaro quale sia il valore che il cliente si aspetta, mentre nel restante 40% c’è solo un’idea vaga e i progettisti lavorano sulla base delle sole esperienze pregresse”.
Il 72% ha un sistema CAD 3D, il 67% un PLM
Un elemento fondamentale approfondito dall’indagine è poi ovviamente la gestione della conoscenza, cioè dei dati, modelli, informazioni e progetti generati nei processi di progettazione e sviluppo, che sono spesso l’asset più critico di un’azienda manifatturiera. “Ciò che colpisce è come quest’area sia mediamente la meno matura tra quelle analizzate”, si legge nel report. I ricercatori hanno approfondito sia l’informatizzazione della conoscenza, sia la sua formalizzazione da tacita a esplicita.
Nel primo ambito il 72% del campione dispone di un modellatore CAD 3D, mentre praticamente tutte le aziende mantengono anche un CAD 2D. Gli strumenti di simulazione (es. CAE, CFD, FEM, ecc.) sono utilizzati in meno del 50% dei casi, e applicativi più complessi (come simulazione a eventi discreti o realtà virtuale) in meno del 20%. Il 67% dispone di una piattaforma di collaborazione, del tipo PDM/PLM. A livello di formalizzazione, quasi il 30% della conoscenza ‘resta’ nelle persone e nella loro cooperazione: il mezzo più usato per scambiare dati e informazioni è lo scambio verbale, seguito da forme semi-strutturate di storicizzazione dei documenti (es. le tipiche cartelle di rete). Gli strumenti IT più strutturati in questo campo (portali intranet, ma anche sistemi PDM/PLM) hanno una rilevanza pari alla metà della comunicazione verbale.
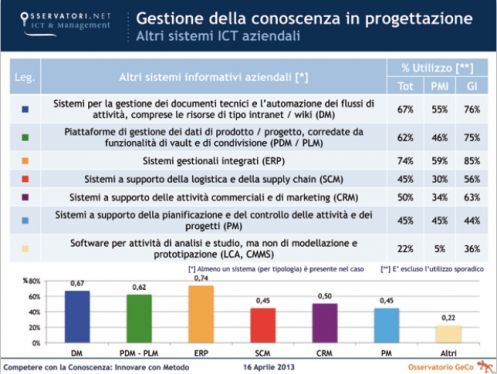
Troppe modifiche: priorità riorganizzare il processo
L’altro grande tema approfondito dall’indagine è quello delle criticità dei processi di progettazione e sviluppo percepite. Al primo posto, segnalate dalla quasi totalità del campione, ci sono le continue richieste di modifica in corso d’opera (94%); il conseguente sovraccarico di lavoro per i progettisti costituisce la seconda criticità (86%), e il frequente superamento del budget stimato si attesta al terzo posto (83%).
Per risolvere questi problemi le aziende stanno pianificando degli interventi, prima di tutto di miglioramento dell’organizzazione e gestione del processo (il 64% li ha già in corso, il 39% li ha realizzati nel recente passato), e poi di introduzione di pratiche e metodologie standard, già avviati dal 57% delle aziende. Segue l’adozione di sistemi PLM per migliorare lo scambio informativo della collaborazione, o di migliori soluzioni di prototipazione virtuale, e infine l’esternalizzazione di alcune fasi di progettazione.
Per le aziende che hanno già introdotto queste soluzioni, i benefici sono indiscutibili. Il 71% ha riscontrato una riduzione dei tempi di sviluppo, il 53% una riduzione dei costi, il 57% un miglioramento della gestione delle attività di progettazione e della loro qualità.
“L’analisi mette in luce un mondo variegato, anche se con alcuni fattori comuni – conclude Monica Rossi -. Prima di tutto, l’alta attenzione per il Concurrent Engineering, sia come parallelizzazione della attività che come collaborazione intra-funzionale, e spesso intra-aziendale; poi la predisposizione per metodi e procedure standard di lavoro, e infine anche il ricorso agli strumenti IT, sia per le attività di modellazione che di scambio dati”.
In questo, aggiunge Terzi, “le PMI rivelano una maturità mediamente rapportabile alle grandi imprese, che sono protagoniste di una competizione globale che sempre più si gioca sulla capacità di generare innovazione e di metterla in pratica in tempi rapidi, cioè di progettare in modo più efficiente ed efficace: un’arte di origine italiana”.