«Il nostro vertice aziendale ha voluto sfruttare fin dal primo momento il Piano Industria 4.0 del Governo. Abbiamo 18 progetti di digitalizzazione in corso, quasi tutti finanziati in parte con incentivi Industria 4.0, o comunque statali o regionali. Il Gruppo storicamente ha sempre investito nell’innovazione tecnologica, vive di questo, ma il Piano Calenda è stato una spinta ad accelerare l’impegno sulla ricerca e sviluppo e sull’innovazione».
Così Pier Luigi Vanti, ICT Corporate Director di IMA SpA, spiega in poche parole il piano di trasformazione digitale del gruppo emiliano, che produce macchine e impianti per il confezionamento di prodotti alimentari, farmaceutici, cosmetici e tabacco.
Who's Who
Pier Luigi Vanti
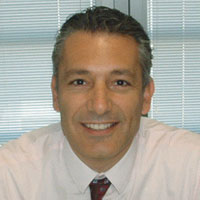
IMA Group è una delle punte di diamante del Made in Italy nel mondo. Qualche mese fa il Sole 24 Ore l’ha classificata tra le cinque “fuoriclasse” italiane degli ultimi 10 anni, sulla base dei dati di crescita, redditività, debito, performance di bilancio e di borsa. Nata a Bologna nel 1961 come produttrice di macchine per confezionare bustine da the – ambito in cui è tuttora leader mondiale con il 70% del mercato – nel tempo si è espansa con acquisizioni in tutto il mondo. Oggi è una multinazionale a conduzione familiare da 1,44 miliardi di euro (fatturato preliminare 2017, cresciuto del 10% rispetto al 2016), realizzati per l’88% all’estero, 5500 dipendenti di cui oltre 2600 all’estero, 41 stabilimenti, e rete di vendita in 80 paesi.
I tre pilastri dei sistemi informativi: ERP, CRM e gestione documentale
Negli ultimi 10 anni IMA ha completato l’implementazione e consolidamento a livello gruppo dei sistemi ERP, CRM, e di gestione documentale, ci spiega Vanti. «Sono i tre pilastri dei sistemi informativi che abbiamo distribuito nel mondo, e ci garantiscono una governance centralizzata dei processi e delle tecnologie. Poi da circa due anni abbiamo avviato i 18 progetti di digitalizzazione di cui accennavo».
Uno di questi riguarda l’integrazione della progettazione. «Il gruppo ha molte business unit, ciascuna specializzata su un mercato, con il proprio ufficio tecnico, che progetta impianti costituiti da diverse macchine connesse con componenti meccanici, elettrici, elettronici e software. Avevamo la necessità di integrare il lavoro di tutti questi uffici con uno strumento globale di gestione e coordinamento dei progetti, per cui abbiamo introdotto un sistema PLM chiamato Palm perché comprende anche la gestione del software applicativo a bordo macchina».
Supply Chain, l’integrazione “SAP-to-SAP” con i fornitori strategici
Un altro progetto riguarda la Supply Chain. «Il 95% della produzione è esterno dell’azienda, noi ci occupiamo direttamente di montaggio, collaudo, validazioni, eccetera. Questo introduce una necessità di coordinamento con i nostri fornitori particolarmente critica e complessa. Quindi da due anni è partito un progetto che nei confronti dei fornitori più fidelizzati e strategici ha previsto un’integrazione nativa “SAP-to-SAP” tra il loro sistema gestionale e il nostro. Mentre con i fornitori meno strategici e non dotati di un sistema ERP l’integrazione avviene attraverso un portale web».
Un terzo progetto riguarda il “virtual commissioning”, per verificare in modo virtuale il corretto funzionamento del software e degli impianti. «Questa verifica si fa al termine della progettazione di ogni gruppo funzionale dell’impianto. Man mano che se ne aggiunge uno, il test diventa sempre più completo. Ed evidenzia non solo i bug del software, ma anche errori di progettazione meccanica che di solito emergono solo al collaudo in officina. In questo modo possiamo anticipare il time-to-delivery di diverse settimane: da 3 a 6 in funzione del tipo di impianto».
Robot, solo per attività a basso valore aggiunto
Poi IMA sta lavorando anche sull’additive manufacturing. «Da anni utilizziamo componentistica di plastica stampata in 3D, ora stiamo verificando la maturità delle tecniche di stampa 3D di componenti metallici, e i rapporti costi/benefici dei vari materiali».
Altro progetto riguarda i Collaborative Robot, cioè carrelli con bracci antropomorfi pensati non come sostituzioni ma come supporti agli addetti dei clienti. «Le nostre linee sono molto manuali e difficilmente automatizzabili, perché ogni impianto è realizzato su specifica e personalizzato. Però possiamo robotizzare alcune attività a basso valore aggiunto che nelle fabbriche dei clienti assorbono fino al 20% del tempo degli operatori».
Per esempio il prelievo in magazzino e la sostituzione di materiali di consumo per l’alimentazione degli impianti. «A maggio è previsto il primo progetto pilota presso un cliente per la sostituzione delle bobine di carta filtro, etichette, filo ecc. su impianti di produzione di bustine da the».
Manutenzione preventiva, imminente il primo progetto pilota
Non poteva mancare poi uno dei fronti più promettenti dell’Industrial Internet of Things: la manutenzione preventiva. «Gli impianti IMA sono sempre stati ricchi di software e sensori, ma finora erano stand-alone, cioè non interagivano attraverso canali digitali né con l’uomo né con altre macchine o sistemi esterni, e poi non avevano sensori “diagnostici”, ma solo sensori legati alla sicurezza e alle performance. Questo progetto colma queste due lacune con una piattaforma di connettività e con sensoristica che consente anche la diagnostica preventiva, per monitorare da remoto lo stato di salute dei componenti critici degli impianti installati presso i clienti».
La tecnologia, selezionata dopo un’analisi di fornitori, system integrator e soluzioni, è Leonardo, la piattaforma IoT di SAP. «Stiamo ormai andando in produzione con il primo cliente pilota, proprio questo mese installeremo in uno stabilimento in Belgio la prima macchina IMA connessa e monitorata da remoto, dal quartier generale del nostro cliente, appunto su piattaforma Leonardo».
Big Data, per ora solo “offline” in laboratorio
In questo caso specifico, precisa Vanti, i dati rimangono di proprietà e nel perimetro societario del cliente. «Per altri invece stiamo realizzando un servizio di control room dove i dati rimarranno a IMA che erogherà a questi clienti un servizio continuativo di monitoraggio e manutenzione preventiva».
Per ora questi dati sono processati con sistemi di analytics “tradizionali”. «Sulla piattaforma Leonardo stiamo raccogliendo dati dagli impianti presso i clienti, che mettiamo in cloud già elaborati e filtrati, quindi non sono grandi volumi. Arriveremo a uno scenario Big Data con il tempo, o decidendo di raccogliere più tipi di dati».
Finora, continua Vanti, IMA ha applicato tecniche di analisi Big Data solo offline, su alcune settimane di dati di comportamento delle macchine raccolti con accelerometri e sensori di temperatura e di grandezze fisiche. «Un lavoro fatto nei nostri laboratori per mettere a punto algoritmi di apprendimento sull’usura di alcuni componenti, da poter utilizzare poi in tempo reale sulle macchine all’opera nelle fabbriche dei clienti».
Connected Field Force per 600 tecnici
Infine l’ICT Corporate Director di IMA cita il progetto Connected Field Force, «molto importante dal punto di vista strategico, perché sta crescendo sempre più l’enfasi sul post-vendita. I nostri impianti hanno un ciclo di vita dai 15 ai 25 anni, la loro vendita resta il nostro business principale ma i servizi di assistenza e manutenzione in prospettiva possono diventare più importanti».
I tecnici IMA lavorano in paesi e zone spesso difficilmente raggiungibili e coperte dalle reti cellulari, quindi usano molta carta e dispositivi offline. «Questo progetto prevede la dotazione ai tecnici di tablet connessi ai sistemi centrali dell’azienda – ERP, CRM e PDM – e con possibilità anche di lavorare offline, sincronizzandosi poi appena il dispositivo può riconnettersi. Stiamo partendo con 40 tecnici di due divisioni pilota. Poi man mano estenderemo alle altre società e divisioni, con un parco utenti a regime di 600 tecnici».
Tre manager per coordinare tutti i progetti
Tutte queste iniziative fanno parte, conclude Vanti, della strategia “IMA Digital” supportata attivamente sia sul piano della comunicazione che su quello dell’organizzazione dai vertici aziendali. «Non c’è un unico manager che fa da “regista centrale”, ma c’è un comitato strategico, che risponde al CdA, e tre figure operative che coordinano tutti i progetti. Uno sono io, che rappresento la parte IT, uno rappresenta la parte innovazione e ricerca di prodotto, e il terzo rappresenta marketing, esigenze dei clienti e comunicazione al mercato».